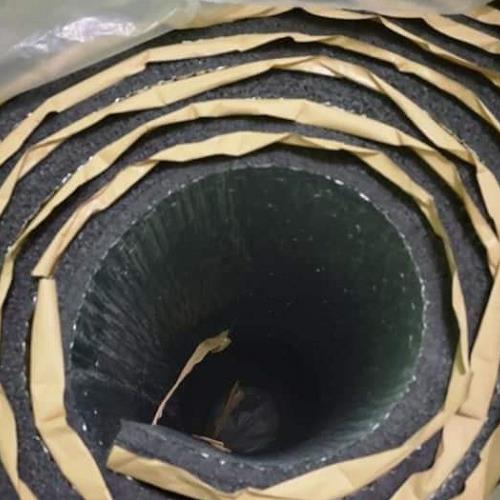
The versatility of polyethylene makes it a product for numerous projects and one of the most used foam materials on the market. While polystyrene is well known for its use in cups and insulation, and the soft and squishy feel of polyurethane foam is familiar to everyone, polyethylene is often a forgotten material. But from packaging and flotation devices, to masonry supplies and shock absorbers, it is hard at work every day, whether we realize it or not.
Polyethylene is a closed-cell foam, which means that its structure is made up of millions of tiny bubbles that are sealed off from each other. This provides water resistance in addition to strength and stiffness that are not present in open-cell foams. It is also resistant to solvents, petroleum products, and is also antimicrobial, inhibiting the growth of mold, mildew, and bacteria. Polyethylene is an elastic material that returns to its original shape after being compressed while still providing adequate cushioning and security where it is needed. It is these properties, combined with its versatility and customization possibilities, that make it so useful in so many applications.
Polyethylene foam sheets, which are formed by heating polymer compounds, are able to have additives added to their formulation to change their properties before being heated and extruded into a solid form. This means that in addition to standard polyethylene sheet foam, there are also anti-static varieties. Antistatic properties aid in the packaging, handling, and shipping of delicate electronics by dissipating static charges that can build up and damage components. The properties of the material remain consistent throughout, as opposed to additives included in the formulation, rather than treatments added after the foam is formed. Like other foams, it is also available in different densities for different applications. The higher the density of polyethylene, the smaller or thicker the cell walls, resulting in a stronger material.
In addition to the performance characteristics that polyethylene can possess, the material also comes in a variety of shapes and sizes. Commonly seen in sheet or plank form, polyethylene has the rigidity to retain its shape when cut into thick sections. They are often used as insulation or for enclosures and custom packaging because, while polyethylene is strong and shock-absorbing, it can also be easily cut into shaped inserts for safely moving or transporting items. Closed-cell foam insulation has excellent moisture resistance, and polyethylene in particular is often used as a thermal insulation material. Polyethylene films are also easily laminated together to form thicker sections that can then be cut into furniture inserts, personal flotation device inserts, or specialized packaging. In addition, support rod polyethylene tubes are made in a variety of diameters for a variety of uses.
Polyethylene rolls are made from very thin materials. This flexibility allows it to be used as insulation wrapped around pipes, seals between foundations and sill plates in buildings, or to make bags or sacks to protect cargo while minimizing space and weight. The style of polyethylene that may be easily recognizable is its cylindrical shape, as it appears every summer as a noodle water toy. These cylinders come in different sizes and can also be used as a support and bracing product to increase personal comfort. When manufactured on a much smaller scale, continuous lengths of polyethylene tube are used in construction as support rods between concrete slabs. The waterproof foam support rods form a cost-effective filler that reduces how much expensive sealing products are needed while allowing for a certain amount of flex between the two slabs by not allowing a three-way bond to form. The support rods allow for expansion and contraction due to weather and temperature changes.